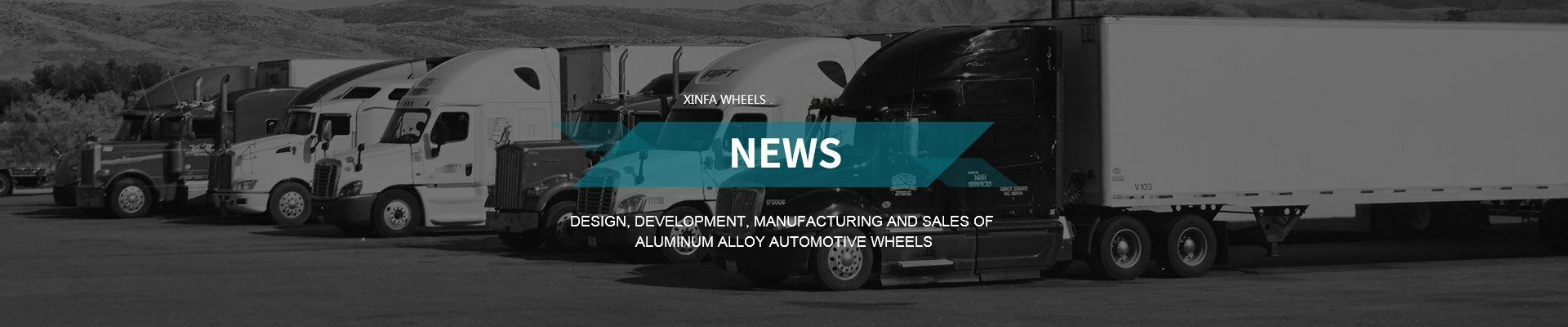
How to keep an Installer from damaging your wheels, what to do when it happens anyway
Publish Time:
2019/01/03
I've seen it happen a million times. A tire shop does something wrong and scratches up a wheel for some reason. Sometimes it's the wrong equipment. Sometimes it's an untrained tech doing something flagrantly wrong. Sometimes it's a great tech having a tool slip at the wrong moment. However it happens, it usually turns into a bad day for all involved. I know it well; not only did it happen in my shop on occasion, but I was also the guy that other installers generally called to refinish damaged wheels when it happened to them.
So while I know all too well that installation damage can never be entirely prevented, there are some ways to easily minimize your risk of damage, as well as ways to deal with it if it does happen.
Of course, if your wheels are already scraped up, much of this will not help you. If you don't really care about keeping your wheels pristine, just that they get you from one place to another you may not want to go to the trouble. But if you're rocking 20” chromies, or any expensive aftermarket wheel, or just if you do care a lot about how the wheels look, it's a small bit of trouble to protect a big investment.
How Wheels Get Damaged
There are a few different ways that your wheels can get damaged while being mounted. The first is what I call a “head drag.” The mounting head is the part that guides the tire sidewall over the lip of the wheel, and so it must lock in place very close to the wheel lip, while not quite close enough to touch.
Some tire sidewalls, particularly on stiff low-profile tires, can exert enough force to flex the head and cause it to touch the wheel, dragging the surface as the wheel turns on the mounter. If the tire tech doesn't notice, this will cause a long scrape against the outer edge of the finish that is quite similar to what we call curb rush, the damage caused by brushing up against a curb.
The second major cause of damage is a “bar snap.” To remove a tire from a wheel, the tech inserts a prybar between the mounting head and the tire sidewall and levers the sidewall up and over the head. When the wheel is then turned the tire can sometimes drag the prybar off the mounting head and slam it down onto the wheel hard enough to chip the paint.
What Not To Do
Let's imagine a scenario here. A new customer comes into an installer. The customer buys a new set of tires and hands over the keys, waits quietly while the tires are installed, settles the bill and leaves. Seconds later the customer comes back and complains to the manager that their wheel has been damaged. Sure enough, one of the wheels has some paint scraped off the outer edge. The tire tech, however, claims that the wheel was already damaged when it arrived. The manager must now make a snap decision based on several factors, but two are the most immediate.
Factor #1: Both tire techs and customers have been known to lie in this situation; the tire tech to avoid responsibility and the customer to scam a shop out of a free wheel repair for that one he curbed last month. Much will depend on what the damage looks like, and how well the manager trusts the tire tech or distrusts the customer.
Factor #2: How are the shop's procedures designed to deal with installation damage? Is there a reporting system already in place for damage when it occurs that shields the techs from honest errors, and takes responsibility for the damage? Or is this an all-too-common occurrence that the shop would rather avoid? Or somewhere vaguely in between?
For a shop, this can be a maddening problem and usually an angry argument no matter which way it goes. For a customer, this is a place you just don't want to be in the first place. That's why this is absolutely the wrong way to go about this.
Proper Prior Planning Prevents Poor Performance
If you want to protect your wheels, you have to lay some groundwork first. You need to choose your shop carefully, and one important factor should be their mounting equipment.
How does it deal with mounting head issues? The newer mounters feature heads made of composite plastic or metal heads containing Kevlar inserts to protect wheel finishes from touches. What you don't want are the older bare-steel head machines that have the most difficulty with low-profile tires. You want your shop to have good equipment, pride in their skill at avoiding negligent damage and procedures in place for dealing with the inevitable accidental damage. You may also want to know that they have the ability to perform or contract high-quality refinishing services if necessary. (See below.)
Depending on how confrontational you want to be, there are a couple of variations on how to prepare for mounting and balancing. The first is to simply take pictures of your wheels before you hand over the car, and tell the manager you have done so. Cellphone pictures are perfect, just get the wheel filling the entire frame so that any damage would be clearly visible and ensure the photos are time-stamped. The second way is to ask a manager to do a walkaround of the car with you while you take the pictures. A good manager might be slightly pissed off by this request. A bad manager will be really pissed off by it.
Either way, the likelihood is that the manager will go back and tell the tire techs some version of, “This [expletive] customer is really [expletive] hardcore about their [expletive] wheels, so be [expletive] careful, you [expletives].” This serves as a wake-up call for the tire techs.
Again, good techs will respond to the implied questioning of their honor. Bad techs will be reminded that they have to pay [expletive] attention this time. Either way, there will be no question of whether the shop is responsible for damage if it does happen.
Finally, make sure you have a spare or some kind of solution available if a wheel needs to be kept for refinishing. Sometimes shops will have loaner wheels, but not very often. When buying aftermarket wheels, especially in exotic sizes, I strongly recommend buying 5 wheels rather than 4 for many reasons, but this potential situation is one of those reasons.
What To Do If It Happens
Stay calm. If you've done the prep work, you shouldn't have any trouble with the shop. Getting mad at the tech isn't going to help. If he's a good tech, he feels bad about the accident anyway. If he's a bad one, he's more worried about his job. Deal with the person who can do something about it and decide whether the wheel will get replaced or refinished.
The easiest and most convenient way for you will be if the shop can order a reconditioned wheel that matches yours. When the wheel arrives it can be swapped for the damaged wheel out at your convenience. You want a wheel from a reputable refinisher like Keystone or CCI that uses only wheels that can be safely repaired, usually called Class “A” cores.
If your wheel can't be easily replaced it will probably have to be refinished. Proper refinishing takes days, not hours. There are any number of mobile services that promise to refinish a wheel in a few hours without ever taking the tire off.
Don't. Just don't.
The issue here is the clearcoat, the hard glossy layer that covers and protects wheel finishes from air and water damage. Mobile repairs simply smooth out and touch up the damaged area and apply a patch of clearcoat. But where that patch comes up against the old clearcoat there is still a microscopic crack where water can still get in. This will eventually destroy the repair.
To properly refinish a painted wheel it is necessary to bring the whole wheel back to bare metal and rebuild the finish from primer to paint to one continuous layer of clearcoat. Polished wheels skip the primer and paint but add the laborious process of polishing. Chrome wheels have to be stripped with acid and dipped in highly toxic liquid metals. To properly prepare and cure clearcoated finishes takes time, from a few days to a week, while chromeplating will require much longer. This will be an inconvenience to you, but if you have a good spare it shouldn't be much more than that.
Owners of Leased Cars
If your car is leased, then regardless of how you personally feel about the cosmetics of the wheels you will still want to do everything possible to protect your wheels and ensure that they are repaired if they get damaged, because most leasing companies will charge you full replacement cost – usually $300-$500 per wheel or more - for any damaged wheels when you return the vehicle.